Inspired by the materials found in oyster and abalone shells, Princeton University researchers have created a new, highly versatile cement composite.
This design mimics the shell’s brick-and-mortar structure, enhancing durability by promoting inelastic deformation and hierarchical toughening.
The newly developed material is 19 times more flexible, can stretch without breaking, and is 17 times more cracking-resistant than regular cement.
According to the team, the results may eventually improve the resistance to cracks in various brittle ceramic materials, such as porcelain and concrete.
Nature-inspired structural strength
In contrast to materials like glass, wood, and steel, cement is brittle and not very flexible without fibers and reinforcements. These flaws restrict its use in structural applications.
A few methods have been tried to improve cementitious materials’ low fracture toughness and ductility by adding polymeric, glass, or metallic reinforcements to cementitious composites. According to researchers, these approaches only result in small increases (about a one-fold increase) in energy absorption and fracture resistance, mostly at the cost of directly changing the materials’ microstructure.
Princeton’s team found that alternating thin polymer and patterned cement paste layers can greatly improve ductility—the capacity to flex without breaking.
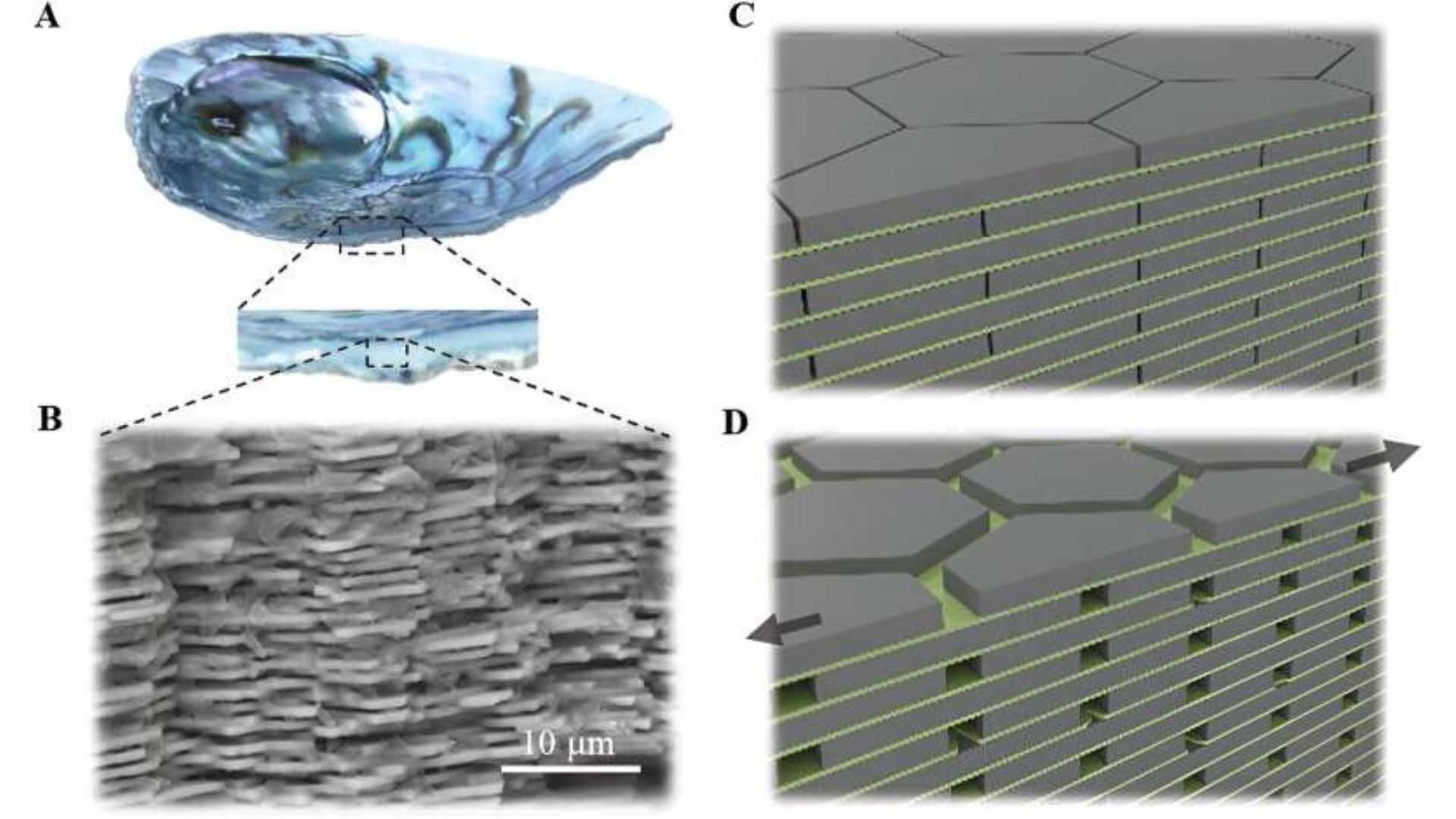
The group drew inspiration for their work on creating materials from biology. In this instance, the group created a composite modeled after nacre, a naturally occurring substance that may be found inside specific shells.
According to researchers, nacre comprises of hexagon-shaped tablets of the hard mineral aragonite joined together at the microscopic level by a soft biopolymer. Its 3D brick-and-mortar structure allows the tablets to slide and the biopolymer to deform, absorbing energy and enhancing toughness.
These mechanisms, along with nano-asperities and tablet interlocking, make nacre resilient despite its brittle components.
“This synergy between the hard and soft components is crucial to nacre’s remarkable mechanical properties,” said Shashank Gupta, a graduate student in the Department of Civil and Environmental Engineering at Princeton University, in a statement.
Novel cement composites
The Princeton researchers used common building supplies like Portland cement paste and a small amount of polymer to create novel composites inspired by nacre.
Layers of cement paste sheets were alternated with polyvinyl siloxane, a highly flexible polymer. By alternating thin layers of polymer with sheets of cement paste, the researchers were able to produce multi-layered tiny beams.
Then, in order to assess crack resistance (also known as fracture toughness), each of these beams underwent a notched three-point bending test.
Researchers created three types of beams: the first with alternating layers of cement paste sheets and thin polymer; the second with hexagonal grooves laser-engraved into cement sheets stacked with polymer layers; and the third with completely separated hexagonal cement tablets connected by polymer, mimicking nacre. These were compared to a solid cast cement paste reference.
Results showed that these composites mimic nacre’s tablet sliding and energy-absorbing mechanisms. Nacre-like-separated composites had 17 times higher fracture toughness and increased ductility by 1791 percent compared to solid cement.
The toughening mechanisms include interlayer deformation, tortuous crack propagation, and tablet sliding. Using laser processing and elastomeric interlayers, this approach significantly improves cement’s mechanical properties while reducing failure risks.
According to researchers, future work can explore diverse soft materials for resilient infrastructure, refine groove shapes for better defect integration, and streamline production methods using integrated lamination-laser processes or additive manufacturing for broader infrastructure applications.
The details of the team’s research were published in the journal Advanced Functional Materials.
ABOUT THE EDITOR
Jijo Malayil Jijo is an automotive and business journalist based in India. Armed with a BA in History (Honors) from St. Stephen’s College, Delhi University, and a PG diploma in Journalism from the Indian Institute of Mass Communication, Delhi, he has worked for news agencies, national newspapers, and automotive magazines. In his spare time, he likes to go off-roading, engage in political discourse, travel, and teach languages.

Daisy Hips is a science communicator who brings the wonders of the natural world to readers. Her articles explore breakthroughs in various scientific disciplines, from space exploration to environmental conservation. Daisy is also an advocate for science education and enjoys stargazing in her spare time.